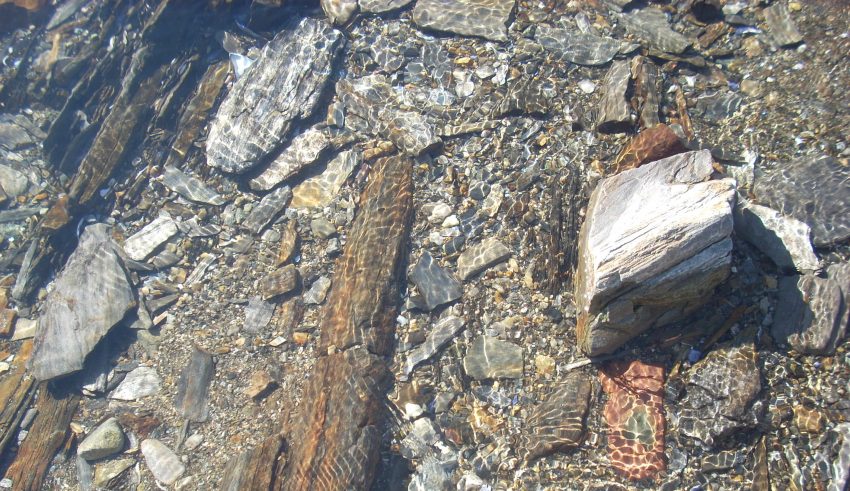
Almost all of the material I read referred to the forensics of the disciplines – a focus on the “How”, including the “tools” of the trade and the “methods” of their leveraging and deployment. One book had an emphasis on “5-S”, another on “VSM”, another on “Kanban”, another on “Kaizen” and so on. One book went at great lengths to talk about the importance of “Flow” and “Roadmaps”. Every book I read made some reference to the miracles performed at Toyota and advocated how they can be replicated in any industry, in any business, anywhere.
Which brings me to the other underlying theme that was shared in everything I read; the “Why”. All of the books and materials I have read and the lectures I have attended have discussed in great detail the benefits of embarking on such programs. All of them create a vision of a better place – a better set of conditions under which a business might operate and the great benefits which will be realized as a result. They all create a very compelling and pretty picture of what the world can be like if only we embrace the disciplines of Lean Six-Sigma as the critical base-line component of any Continuous Improvement Program.
And most of the books and content also address the remaining Six Honest Serving Men of Rudyard Kipling including; “What”, “When”, “Where” and “Who”.
All of this knowledge and instruction is necessary, well and good. I would support any argument that it is important to know how to properly use the tools in your toolbox; which one to grab under any given circumstance and how to wield it and where for maximum effectiveness. I would also support the vision painted by the proponents of such knowledge of what could be achieved.
However, the one thing I noticed in almost all of the material I reviewed – very subtle in nature, but with a profound and devastating impact on the results – was the consistent references to the singular.
There were many mentions of “you”, “me” and “I”; but very few referred to “we”, “us”, “them” or “they” – not to mention “the team”. It is almost as if any results that might be achieved in a Continuous Improvement program are solely the consequences of an individual’s efforts and not that of a coordinated effort of many – not to mention an entire company. There was even considerable reference in the “assumptive” such as; “then this is done, followed by that, to achieve the goal” – as if it were all going to magically happen without human involvement at all. If leadership, program management and communication skills are mentioned at all, they are usually given short shrift and tucked towards the back of the book.
When I look at a traditional organization from a Continuous Improvement perspective; I see four major stratifications of people involved and their respective roles – each a distinct and necessary member of an overall traditional Continuous Improvement Team, but whose deliberate integration is required to be successful.
Download Article 1K Club